In the Weir Group Capital Markets Event presentation last week, Chris Carpenter revealed that the company was collaborating within its divisions on trials of ore sorting technology in an effort to move less rock at mine sites and optimise processing within the plant.
Carpenter, Vice President of Technology at Weir ESCO, said the company was combining Motion Metrics’ particle size distribution (PSD) capability with ore characterisation technology to explore “in-pit sorting” opportunities for its clients. Rock Teeth For Backhoe

“Looking further out, we believe ore characterisation and in-pit ore sorting has the potential to transform mining by moving less rock, using less energy and creating less waste,” he said during his presentation. “Ore characterisation technology, which is underpinned by sophisticated sensing systems, captures critical data on properties and composition of rock, including rock hardness and mineral and moisture content.
“When coupled with Motion Metrics fragmentation analysis technology, it has the potential to be a game changer, giving miners a full picture of the size and characteristics of rocks.”
Motion Metrics, a developer of artificial intelligence (AI) and 3D rugged machine vision technology, was acquired by Weir almost a year ago, with the business incorporated into the Weir ESCO division. Its smart, rugged cameras monitor and provide data on equipment performance, faults, payloads and rock fragmentation. This data is then analysed using embedded and cloud-based AI to provide real-time feedback to the mining operation.
These technologies were initially developed for ground engaging tool applications but have recently been extended into a suite of products and solutions that can be applied from drill and blast through to primary processing.
Carpenter said the added PSD capability from Motion Metrics was expanding the company’s value presence across the mine to the processing plant, where Weir Minerals operates.
“Results from early adoption of Motion Metrics PSD solutions have been extremely encouraging,” he said. “Feedback from customers is positive; data sharing and collaboration have increased.
“Given this early progress, we are really excited about the opportunity and expect fragmentation analysis to be a key growth driver for Motion Metrics in the years to come.”
On the in-pit sorting potential, Carpenter said Weir ESCO had laboratory-validated equipment and field trials of its proprietary solution that were due to start at customer sites before the end of the year tied to these developments.
“If successful, this technology opens the door to in-pit sorting, where miners complete the first stage of crushing in the pit and analyse the outputs to make real-time decisions about which rocks have sufficient mineral content to be moved,” he said. “This is a step change from the current process, where energy is expended in transporting and processing all of the rocks, regardless of mineral content, and with significant waste generated from zero- and low-grade material.”
He concluded: “Our vision is to move less rock, moving only the rocks with sufficient mineral content and using the data that is captured on size and hardness to optimise processing. The natural evolution thereafter will be towards real-time automation control of processing equipment, ensuring the right rocks are processed in the most efficient way, using less energy and creating less waste.”
The Weir Group says it has completed the acquisition of Carriere Industrial Supply Limited (CIS), a manufacturer and distributor of highly engineered wear parts and aftermarket service provider to Canada’s mining industry.
Its products, which include mining buckets and lip systems, help customers increase productivity through reduced downtime and improved safety, Weir says. The enterprise value for the transaction, which will see CIS join the ESCO Division, is £20 million ($26 million), subject to customary working capital and net debt adjustments.
The transaction builds on long relationship with CIS, acting as ESCO distributor in Eastern Canada for many years, Weir said, while delivering on ESCO’s strategy to have direct sales channels in major mining markets. It also increases ESCO’s capability in underground hard-rock mining applications, with CIS having a strong presence in gold and being located close to deposits of nickel and lithium.
According to Weir, the acquisition will be earnings- and margin-accretive in year one with returns expected to exceed the group’s cost of capital in the first full year of ownership.
Andrew Neilson, President of Weir’s ESCO Division, said: “The acquisition of CIS aligns with our strategy of providing direct sales and service to our mining customers and builds on our long-standing partnership, while also enhancing our capabilities in underground hard-rock mining applications.”
Weir Minerals has launched the new Multiflo® Mudflo™ hydraulic submersible slurry pump, engineering the pump to, it says, tackle abrasive applications and large particle handling.
The Multiflo Mudflo pump features a hydraulically driven wet-end specifically designed to efficiently and safely reprocess and relocate tailings ponds, maintain water retention dams and manage slimes and sludge ponds.
It combines the Warman® MGS pump-end, Multiflo CB32 hydraulic cutters and ESCO® excavation teeth to provide efficient pumping of highly charged and abrasive slurries, the company claims.
Weir Minerals’ Ultrachrome® A05 chrome alloy impeller ensures high wear resistance and the specially engineered suction strainer minimises the risk of clogging by preventing large solids and debris from entering the pump. Drawing on decades of Warman pump design experience, the Multiflo Mudflo pump is capable of pumping between 150 cu.m/h and 1,200 cu.m/h, up to 82 m head.
The Multiflo CB32 hydraulic cutters feature the ESCO Ultralok® tooth system to prevent premature breakage, avoid tooth loss and protect the integral locking system to ensure the continuous operation of the pump, it says.
Engineered by the Weir Minerals dewatering pump experts in Australia, it is available for global customers from July 2021.
Cameron Murphy, Director of Dewatering Weir Minerals APAC, said: “The Multiflo brand is synonymous with high quality and long-lasting equipment. In designing the Mudflo pump, our dewatering experts drew from the very best Multiflo, Warman and ESCO technology and used advanced hydraulics to create an innovative and cost-effective new solution for mine dredging applications.”
The product was developed following close customer collaboration and a mutual commitment to safety and technical excellence, Weir Minerals said.
Geoff Way, Weir Minerals Dewatering Specialist, said: “It is not uncommon for sites to use a combination of pumps, shovels, excavators and trucks for dredging applications. When one of our long-time partners in Indonesia contacted us about developing a custom solution for the slurry build-up in their sumps, we knew we could provide a better solution. We are problem solvers. We considered our customer’s pain points and engineered a new solution to efficiently and safely manage their site processes.”
The Multiflo Mudflo pump can also be retrofitted to competitor OEM equipment, Weir Minerals says, with the quick-hitch plate attachment ensuring convenient installation and removal from hydraulic excavators.
The Multiflo Mudflo pump can be assembled on land, eliminating the safety risks associated with assembling pumps over water. Furthermore, the new hydraulic hose management system reduces the risk of hose entanglement and trip hazards, all the while providing a reliable hose bend radius to ensure smooth oil flow.
Weir Minerals has released a new Isogate® WR knife gate valve to reduce cycling discharge while improving wear life.
The lightweight, long-lasting Isogate WR knife gate valve offers miners and aggregates operators alike a step change in valve performance, according to Weir Minerals.
The release came on the same week Weir Group announced its 2020 financial results, which saw the company report revenue and adjusted operating profit of £1.97 billion ($2.73 billion) and £305 million from continuing operations, respectively. These figures were down 4% and 3%, respectively, from 2019 totals.
On the new valve, Weir said: “Incorporating the latest advances in design and materials technology from Weir Minerals’ expert engineers, the range of Isogate WR knife gate valves are more reliable, while producing minimal fluid discharge and weighing considerably less than equivalent mining valves.”
John Abbott, Global Product Manager – Valves & Tailings, said: “Drawing on decades of wear analysis, we’ve optimised the Isogate WR knife gate valve’s body design, by reinforcing the areas subjected to the harshest wear and pressure. At the same time, we have reduced the weight elsewhere to produce a robust, long-lasting mining valve that’s significantly lighter than comparable products.
“The weight reduction can be especially significant in situations where a number of valves are used on a specific installation, such as in a hydrocyclone cluster, or where lightweight piping systems are used.”
The gate has also been redesigned, with stronger materials resulting in a thinner gate that can still withstand the pressure of mining slurries. This combines with the valve’s unique gate guide that, Weir says, reduces deflection by ensuring smooth gate movement and less strain on the sleeve elastomer during blade transition.
The Isogate WR knife gate valve uses Weir Minerals’ new Isogate WSL sleeve, which comes with proprietary Linard® HD 60 silica-reinforced natural rubber to solve the three most common problems with sleeved knife gate valves: leakage during cycling, tearing and load distribution ring (LDR) failure due to corrosion and erosion, the company explained.
Leveraging the Linard HD 60 rubber’s high resilience against cut, tear and abrasive wear to improve wear life, the new Isogate WSL sleeve fully encloses the LDR to prevent corrosion. By allowing the rubber to move with the blade cycles, the design reduces the chance of tearing while reducing slurry discharge by up to 75%, according to Weir.
The Isogate WSL sleeve can also be used in existing Isogate WS knife gate valves, improving wear life and decreasing discharge on cycling.
Abbott added: “When designing the Isogate WR knife gate valve, we focused on features that improve the everyday experience of working with our valves. This includes important things like improved grease distribution and improved body flushing when used on high solids concentration applications.
“In-depth finite element analysis enables us to ensure the product’s integrity, while making it lightweight. There are also a lot of smaller features to make life easier, such as a larger grease reservoir, ISO mount standardisation and an external visual indicator for the valve’s status.”
Other notable developments from Weir Group’s 2020 financial results included the first order for ESCO’s ToolTek™ system.
This collaborative effort with key mining customers provides enhanced safety for maintenance personnel during the replacement of worn Nemisys® points and adapters, according to ESCO. It features a hydraulic crane mounted tool that is remotely operated, well out of harm’s way during the replacement of worn components. New parts are pre-staged on racks positioned on the flatbed truck outfitted with the hydraulic crane. The truck also features a recycle bin for safer disposal of worn parts.
Alongside this, Weir said in 2020 it installed the first pilot Terraflowing® plant at a customer’s mine site designed to cost-effectively reduce water in tailings, enabling this waste product to be safely stored or repurposed.
Terraflowing incorporates a two-stage cyclone dewatering process followed by centrifugation of the final stage of cycloning overflow. In the process, three dewatered tailings streams are produced: a primary cyclone underflow, a secondary cyclone underflow and a centrifuge pulp. These three streams can be combined or used in different configurations depending on the end use of the tailings stream, according to Weir Minerals.
This three-stage system offers the flexibility to make provision for variations in mineralogy and particle size distribution as well as the opportunity to recover ‘tailings as a resource’, it added.
Weir Group says its ESCO division is working on an innovative solution that automates ground engaging tool (GET) changeouts, helping improve safety on mine sites.
In its annual report, released today, Weir said the GET Toolhead® would reduce the need for personnel to be in the pit, one of the most hazardous areas of a mine.
The new automated toolhead turns a hydraulic manipulator into a robot arm, according to Weir. It can securely grip and move GET, allowing it to replace parts weighing up to 500 kg.
“The movement of the toolhead is controlled remotely by a single operator, compared to teams of up to three people who would normally be required for a manual change out,” the company said.
Weir said in the report that it was continuing to commercialise this automated offering.
ESCO says it is introducing the Nemisys N70 Lip System for hydraulic excavators as it looks to expand the tooth system’s reach beyond the large mining shovels, large excavators and wheel loaders it was initially developed for.
The Nemisys tooth system is a field-proven performer with installations on over 500 machines worldwide, ESCO, which was acquired by Weir in 2018, said. It helps reduce maintenance costs through improved reliability, faster and safer replacement, and improved lip coverage.
The N70 lip system features an integrated single-side lock for easier and faster removal to minimise machine downtime during maintenance cycles. The hammerless lock provides improved engagement with the nose to significantly reduce the chance of point loss and unplanned downtime. Adapters, meanwhile, feature a triple wear cap system to protect both legs.
The Nemisys N70 components are available to upgrade existing buckets to the premier ESCO system for exceptional performance and a lower cost of ownership over conventional lip systems, the company said.
ESCO is a leading designer, manufacturer and provider of highly engineered wear and replacement products and services essential to the performance of our customers’ equipment used in mining, construction and industrial applications.
The Minerals and ESCO divisions continued to stand out in Weir Group’s half-year 2019 financial results, with the two mining focused segments now representing around 75% of group revenues.
The Weir Group recorded revenue of £1.3 billion ($1.6 billion) in the first six months of the year, up from £1.07 billion a year earlier prior to the ESCO acquisition. Operating profit, meanwhile, was £172 million, up 25% year-on-year, with the Minerals division posting an operating margin of 17.2% and ESCO recording a margin of 14.1% (up 300 basis points from a year earlier).
In addition to Minerals and ESCO now commanding some 75% of group revenues, the two’s recurring aftermarket sales also now represent about 80% of total revenues.
In the first half of 2019, Minerals orders grew 5% with aftermarket orders up 8%, reaching record levels, according to Weir. “Original equipment orders, which are traditionally lumpier, fell by 2% year-on-year, but returned to growth in Q2 (June quarter) and this is expected to accelerate in the second half,” the company said.
ESCO, meanwhile, recorded a 5% increase in pro-forma revenues to £280 million, with annualised cost savings of $20 million ahead of schedule when it comes to the company’s medium-term target of achieving $30 million synergies.
During the period, original equipment demand within the Minerals segment benefited from miners continuing to expand current operations and investment in new mines, with demand for new technologies that increase efficiency and sustainability while lowering total costs, Weir noted.
This included strong demand for the company’s Enduron® HPGR (high pressure grinding roll) technology that reduces water and energy consumption, the company said, adding that the company had been contracted to support a large greenfield development in the UK in the period.
Weir said it also saw growing interest in its Terraflow® solution to enable tailings waste to be cost-effectively recycled or repurposed. This equipment brings wet tailings down to 90% solids paste to be pumped into a containment area or used for paste backfill.
The company added: “Aftermarket demand was strong, due to production growth and structural trends. These include continued ore grade declines that increase the amount of rock that needs to be processed, intensifying wear and tear and leading to additional demand for spares and services,” the company added.
During the period, Weir also added a new Minerals service facility in Alaska, which, it said, gives the division the ability to rapidly respond to demand for spares and services and is a “key differentiator in need-it-now mining markets, where production intensity is increasing, and the costs of unplanned downtime are significant”.
The company’s technology work continued to focus on incremental innovations and “Mine of the Future developments” aimed at solutions that are smarter, more efficient and sustainable, Weir said. This included focusing research and development on new pump and alloy designs, digitisation, ore hoisting, hybrid separation and tailings management.
Weir ESCO benefited from the same macro mining trends as its Minerals segment including increased ore production and the focus by mining customers on optimising productivity, the company said.
“This supported demand for differentiated technology that is proven to sustainably increase efficiency,” it said. The first half of the year saw early market share gains for the N70 Nemisys® lip system, which extends the division’s Nemisys technology – featuring a cast or plate lip with shrouds and a three-piece tooth system. This is currently being trialled on smaller machine classes including wheel loaders, Weir said. “The N70 improves customer productivity through increased wear life, lower fuel consumption and reduced maintenance costs.”
The company also launched its GET Detect System during the period, an innovation it worked with Australia’s Mining3 on that provides instant feedback to the machine operator if one of the ground engaging tools used to extract minerals is lost or damaged.
The Weir Group says it is investing an additional $15 million in its Newton manufacturing facility, in Mississippi, US, as part of a total $50-million plan to support an additional 150 jobs at the ESCO division plant.
When the investment programme is complete, employee numbers will be more than 400, a 60% increase from 2016, Weir Group said.
The Newton facility, one of Weir’s largest manufacturing operations, produces ground engaging tools for mining and infrastructure needs and was brought into the group with last year’s acquisition of ESCO. The expansion is slated to be complete by August 2019, Weir Group said.
Weir Group CEO, Jon Stanton, said: “The equipment we make in Mississippi is exported around the world and the increased demand from our mining and infrastructure customers gives us great confidence in the future.”
The Mississippi Development Authority (MDA) is providing assistance for workforce training, as well as statutory tax exemptions, according to Weir.
MDA Executive Director Glenn McCullough, Jr, said: “The Weir Group’s ESCO division with its talented employees show the world each day that global manufacturing leaders find the people and place needed for success in Mississippi. For nearly 50 years, ESCO’s workforce has enabled the company to achieve its goals by producing top-quality mining equipment used around the world, and this continued corporate investment demonstrates Weir’s commitment to doing business in our state.”
Approximately 80% of the products manufactured at the Newton facility are exported. This makes Weir’s ESCO division the world’s leading supplier of ground engaging tools for the mining industry, Weir said. The facility began operations in Newton in 1971.
Mining3 says an innovative tramp metal detection system – built into the bucket of mining equipment – is nearing commercialisation.
The company has been working on the new technology over the past few years subsequent to safety concerns and crusher damage caused by tramp metal such as bucket teeth, drill bits, tools and more, often remaining in mined material, it said. This can cause a loss of production and pose a significant safety threat to operators and maintainers.
Mining3 is working with Weir ESCO, an equipment metal parts manufacturer, for the incorporation of the uncrushables technology into its bucket design and will facilitate the commercialisation of the technology, Mining3 said.
“With the new patented uncrushables detection system, obstructive tramp metal can be identified and diverted before reaching the processing plant,” Mining3 said. “A pulse induction metal detector embedded inside the large steel bucket of a digging machine takes on the difficult task of detecting metal items scattered throughout the material. The system’s variable sensitivity is tuned for an object’s target size, focusing on larger, more obstructive uncrushables and allowing for the removal of smaller items further down the processing line. Further, the detection algorithm accommodates changes in ore grade and identifies the type of object.”
When metal is detected, the operator is alerted in real time, allowing for the necessary next steps – usually the dumping and diverting of the material, Mining3 said. In addition to the operator alert, the system integrates into a control centre interface and allows remote management and monitoring of the process.
The tramp metal detection approach requires minimal sensing equipment in the bucket and commercial versions will discreetly integrate the coil into the design, according to Mining3.
Successful site trials have led the project to integrate with larger and more technical machinery. Current prototypes are installed on Komatsu WA1200, Cat 992K, 993K and 994K machines operating on run-of-mine stockpiles in iron ore, gold and copper mines across the globe. Mining3’s research is now focused on deployability, robustness and optimisation, it said.
The Weir Group has entered into an agreement to sell its Flow Control division to First Reserve, a global private equity investment firm focused exclusively on energy, for an enterprise value of £275 million ($360 million).
Weir, which will receive cash for the sales, said all the way back in April 2018 that it planned to sell the division. The admission came alongside the acquisition of ESCO. The transaction remains subject to certain regulatory and other approvals, with completion expected in the June quarter, the company said.
The Flow Control division primarily provides highly engineered pumps, valves and other solutions used in power, industrial and downstream oil and gas applications, according to Weir.
Weir said: “Once this transaction completes, on a pro forma basis, more than 80% of Weir’s revenues will be from attractive aftermarket-intensive mining and upstream oil and gas markets.”
Weir Group CEO, Jon Stanton, said: “The decision to sell Flow Control is part of Weir’s recent portfolio transformation which focuses the group on where we can maximise long-term value – building on our strong global leadership positions in mining and upstream oil and gas markets.”
Jeff Quake and Neil Hartley, Managing Directors of First Reserve, said: “In our view, Weir Flow Control represents an attractive growth platform in a fragmented sector, with internationally recognised brands driven by recurring high-margin aftermarket parts and services which have proven to be resilient through multiple economic environments.”
After the sale completes, Flow Control will continue to be led by current President David Paradis and his management team, Weir said.
In the year to December 31, 2018, Flow Control’s unaudited financial results included profit before tax of £23 million on a pre-exceptional items and intangibles amortisation basis.
International Mining Team Publishing Ltd 2 Claridge Court, Lower Kings Road Berkhamsted, Hertfordshire England HP4 2AF, UK
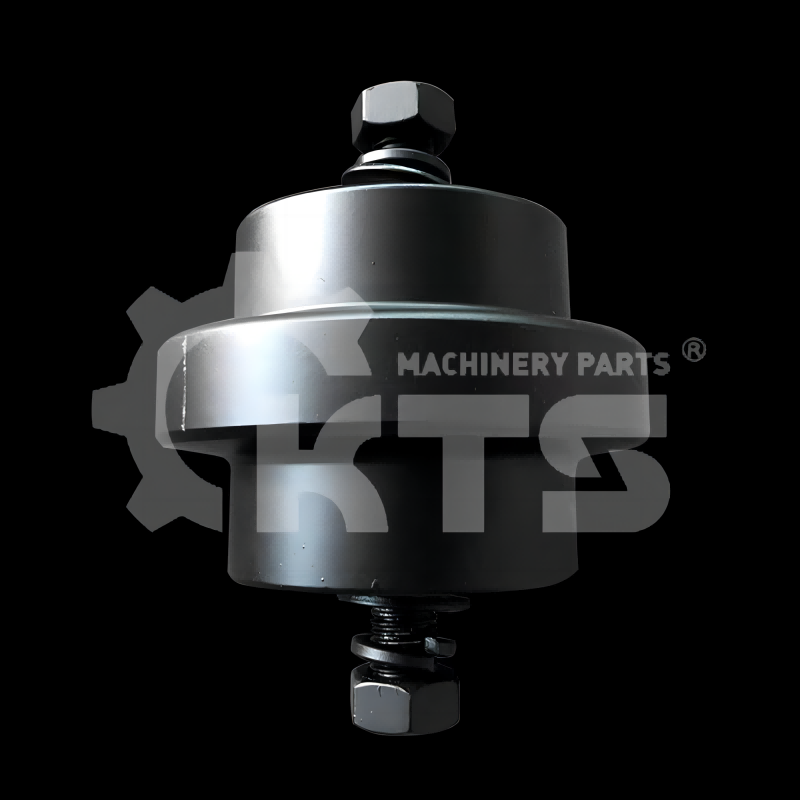
Digger Bucket Pins Tel: +44 (0) 1442 870 829 Fax: +44 (0) 1442 870 617 Email: [email protected] or [email protected]